Bigfoot system tools
POLISHING SYSTEM TOOLS
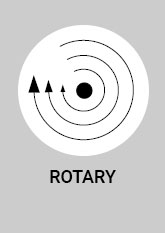
ROTARY
A rotating disc, rotates on a central axis with the highest velocity being at the pads edge. Rotary tends to be the most invasive movement on the surface, generating substantial friction and heat which can lead to burns, strike throughs, and rotary induced swirl marks if used improperly.
In the hands of a skilled technician a rotary tool features the lowest vibration levels of any tool movement, but can take a great deal of time to learn to use the tool properly.Rotary movement is most commonly used for polishing operations.
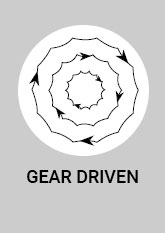
GEAR DRIVEN
The backing plate follows an orbit (the scope of which depends on the distance between the rotation axis of the drive shaft and the central axis of the rotor disc) and is at the same time constrained to rotate about its own central axis (typically due to the inclusion of a gearing).
The number of orbits at each revolution of the disc is always constant and depends on the parameters of the gearing used. The gear movement is more aggressive on surfaces with respect to the random orbital movement and generates a generally higher vibration level.
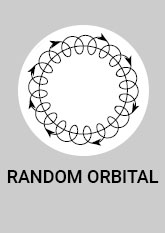
RANDOM ORBITAL
the backing plate follows an orbit (the amplitude of which depends on the distance between the rotation axis of the drive shaft and the central axis of the backing plate) and is free to rotate about its own central axis. The backing plate is free to rotate at varying velocities and directions by effect of the centrifugal force of the offset movement and by effect of friction.
Should the friction forces be such as to prevent rotation of the disc while the tool is still operating, the random orbital movement would simply become an orbital movement. The number of disc rotations is variable and independent of the number of orbits performed.
The random orbital movement is at present the best compromise in terms of effectiveness and surface treatment quality.
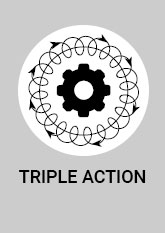
TRIPLE ACTION
Rupes is offering a new type of movement known as Triple Action. The power of a motor can be expressed as the product of the torque multiplied by the velocity. During normal use of a tool, the operator applies a variable load, which by effect of the friction forces and the work carried out by the motor might be such as to reduce the number of revolutions of the motor. The load applied by the operator during normal use of a tool varies significantly over a measure of time, causing large variations in velocity of the number of orbits and the rotation of the rotor disc and consequently reducing the uniformity and effectiveness of the work operation. A more homogeneous process leads to a significant reduction in working times.
In the case of triple action tools, and similar to the movement of random orbital tools, the disc follows an orbit and is free to rotate about its own central axis but, thanks to a special epicyclic gear reducer located in front of the cam group, the torque value is significantly increased while at the same time the velocity is reduced. With the use of this solution the impact of a variable in performance (the load applied by the user) is substantially minimized and, consequently, a greater uniformity of performance of the tool. This provides a considerable improvement in the surface finish as well as a drastic reduction in the vibration levels.
From the very first use it is clear how advantageous this configuration is in terms of effectiveness and vibration reduction all thanks to the introduction of the epicyclic gear reducer; this is a technical improvement that so profoundly improves and changes the functionality of the tool that it merits a new movement category, the TRIPLE ACTION.
Perfect Results
Achieving polished perfection on a surface as efficiently as possible is the primary goal of the BigFoot project. BigFoot simplifies the polishing process, substantially reducing time and producing the optimum result. Thanks to the complete range of polishers, pads and compounds, all designed to work in synergy, BigFoot’s innovative system based approach guarantees exceptional results in less time for virtually any polishing application.