BigFoot Polishing System – Polishing Pads
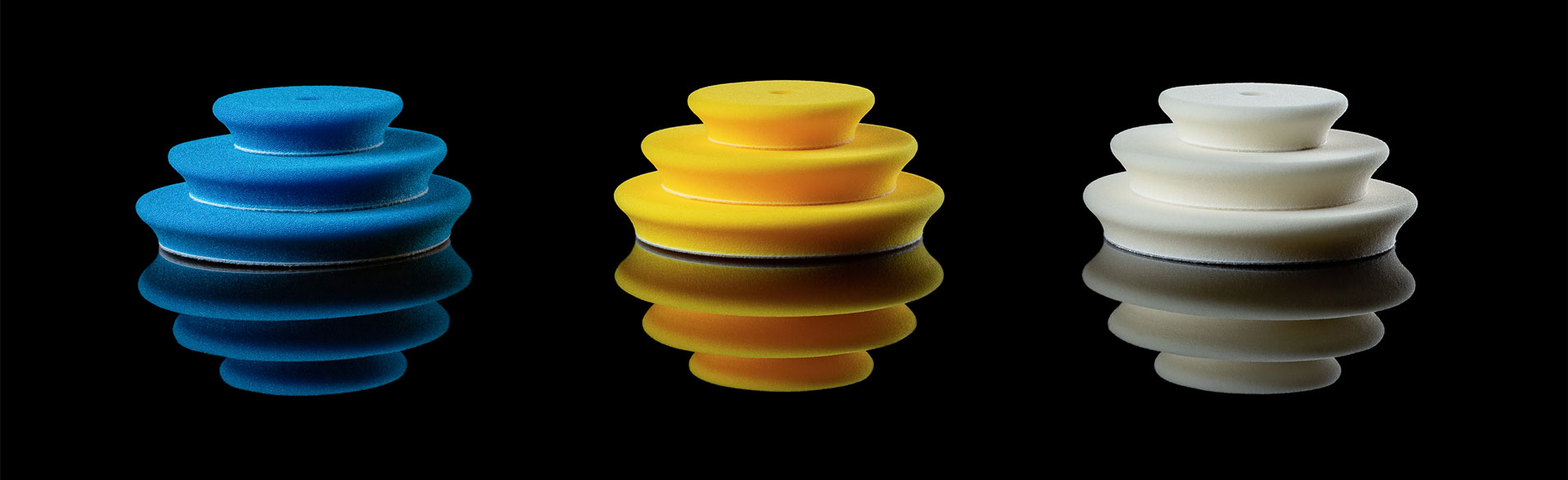
-
FOAM
-
WOOL
-
MICROFIBER
BIGFOOT FOAM POLISHING PADS
- D-A FOAM
- ROTARY FOAM
D-A FOAM POLISHING PADS
BLUE FOAM PAD COARSE
The D-A COARSE foam pad is specially designed to be used with both random orbital and gear-driven tools. The unique open-cell foam material removes mild to severe defects from most paint systems when paired with RUPES DA-COARSE compound.
YELLOW FINE FOAM PAD
The D-A FINE foam pad is the most versatile foam pad in the RUPES BigFoot range, delivering an effective rate of defect removal and capability for high-gloss finishing on most paint systems. Pair with RUPES DA-FINE polishing compound for moderate to fine defect removal, paint refinement, or final finishing after heavy compounding steps.
WHITE ULTRA-FINE FOAM PAD
The DA ULTRAFINE foam pad is our finest grade of foam, designed for ultra-high gloss finishing and polishing haze-prone or very soft paint surfaces. The unique material composition of the DA ULTRA-FINE pad can also be used for the application of sealants or waxes when no correction is required. Pair it with UNO PURE ultra-fine universal polish to remove extremely fine defects or to bring out a show car level finish on even the most difficult-to-finish vehicles.
ROTARY FOAM POLISHING PADS
BLUE FOAM PAD COARSE
The high performance and aggressive blue foam removes severe defects and sanding marks on painted surfaces.
YELLOW FOAM PAD FINE
Eliminates moderate surface defects and imperfections while restoring high gloss. The new foam structure provides a smooth and comfortable polishing experience.
WHITE FOAM PAD ULTRA FINE
The completely new soft foam technology removes fine imperfections and creates a unbelievably high gloss finish. Highly recommended when using rotary on dark colors.
WAFFLE COARSE FOAM PAD
The WAFFLE COARSE FOAM PAD is the coarsest of our Rotary Waffle Pad range. Made of a blue foam material, this pad provide high performance and aggressive removal of severe defects and sanding marks on painted surfaces.
WAFFLE FINE FOAM PAD
The WAFFLE FINE FOAM PAD can remove moderate surface defects and imperfections while leaving an excellent finish. The new waffle pad surface provides a smooth and comfortable polishing experience.
WAFFLE ULTRA-FINE FOAM PAD
The WAFFLE ULTRA-FINE FOAM PAD is designed to remove fine imperfections and create an unbelievably high gloss finish. The waffle pad face, perfect against the stress caused by rotary motion, offers a great stability when correcting paint defects or removing haze left by previous heavier polishing phases.
BIGFOOT WOOL POLISHING PADS
The Wool Polishing Pads have a great cutting range, an excellent finish, they are slightly less aggressive than microfiber, but they are one of the best choices in terms of cutting defects especially as a first of two steps or for one step applications.
In the RUPES BigFoot range we have two categories of wool pads, each of them specially designed for a specific polisher movement; D-A Wool Pads, for Random Orbital and Gear Driven Orbital, and Rotary Wool Pads.
The D-A Wool Polishing Pads are available as D-A MEDIUM and D-A COARSE, while the Wool Polishing Pads for Rotary are divided in Twisted Wool Pads and CUT & FINISH Wool Pads.
- D-A WOOL
- CUT & FINISH ROTARY
- TWISTED WOOL FOR ROTARY
D-A WOOL POLISHING PADS
D-A COARSE WOOL POLISHING PAD
All the pads in the coarse wool range are constructed using two distinct fiber lengths creating a dual density wool surface and a specific visible pattern. More than just an aesthetic detail, this configuration provides a great balance of cutting power and finishing ability when compared to traditional or single density wool pads.
D-A MEDIUM WOOL POLISHING PAD
The yellow medium wool pad range features a consistent 15mm fiber length through the entirety of the pads surface. This soft and flexible wool, paired with a soft and flexible yellow foam backing, provides excellent cutting of moderate defects, excellent finishing ability on most surfaces.
CUT & FINISH POLISHING PADS FOR ROTARY
The CUT & FINISH Rotary Wool Polishing Pads represent a massive leap forward in rotary pad technology, providing versatility for detailers, body shop technicians, or anywhere a rotary polisher finds frequent use.
These pads use only the highest-quality genuine merino wool fibers refined to a consistent 20mm length, assembled in an extremely dense pattern onto a specially designed foam interface.
TWISTED WOOL POLISHING PADS FOR ROTARY
Designed to provide impressive cutting speed, reduced risk of rotary swirls and improved process efficiency while maintaining a smooth, vibration-free, and operator experience.
The all-new RUPES twisted natural wool pads for rotary are available in three sizes and are compatible with virtually all rotary polishing tools on the market today. Each RUPES twisted natural wool pad is constructed of a premium blend of 100% natural lamb’s wool and assembled with a precise strand length of 35mm.
No synthetic fibers or fillers are used in the construction of the pad and each strand is steam set to ensure consistency and fastness of color.
The RUPES’ twisted natural wool pads were developed to optimize the performance of RUPES Coarse Rotary Compound in a variety of applications and industries.
MICROFIBER POLISHING PADS
For Random Orbital
The innovative RUPES PATENTED microfiber polishing pads are manufactured using a polyurethane resin directly injected into the structure between the Velcro interface and the microfiber fabric. The resin crosslinks directly to both materials to provide a stable and secure bond without the use of adhesives.
Due to the unique moulding technique, RUPES is able to offer a pad with a beveled, allowing easy conformability to all shapes during the polishing process. In addition to helping dissipate heat, the centre hole also helps to correctly fit the microfiber polishing pad onto the backing plate.
These pads provide Quick defect correction on high solids or ceramic clears coat. High efficiency on clear coat and one stage surfaces.
Greatly reduced polishing cycle times. Less dust on the surface during polishing process. Comfortable and easy to use.
BLUE COARSE MICROFIBER POLISHING PAD
The coarse microfiber pads are designed for removing heavy swirl marks, scratches and oxidation from any painted surface. The cutting version, perfect to use with the high performance D-A COARSE polishing compound, allows for the true correction power of the product used and for maximum product coverage to achieve the highest quality results on even the hardest standard and scratch-resistant paints of all colors.
YELLOW FINE MICROFIBER POLISHING PAD
The Fine Microfiber Pads are designed to restore the depth and clarity to your vehicle’s paintwork. The high-density microfiber is perfect for removing light swirl marks and holograms using fine BigFoot polishing compound. The Fine Microfiber Pads eliminate light imperfections delivering a perfect optical grade finish.